The Evolution of IoT: And Why Hardware Will Continue to Drive It
By Mike Bolduc | October 31, 2017
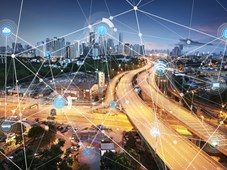
When we think of the Internet of Things (IoT), we think of devices connecting to each other without wires, cables or physical contact. The promise of these devices is that the information they provide and actions they make possible will make peoples’ lives easier and more efficient.
The IoT has created opportunities across industries, from medical and automotive to aerospace and utilities. No matter how small or smart products become, however, hardware will always be a driving force behind the scenes. After all, we wouldn’t even be able to turn on our smartphones or power our connected home devices without a hardware component or switch.
Some of our most-used devices, from our iPhones to our FitBits, highlight the importance of physical components to keep us connected. Not only does the hardware itself allow for people to establish a physical bond with a device, but the tactile connection communicates a brand’s identity and perceived quality. In fact, a product’s user interface will often determine how it sells, and in some cases, can even be a key contributor to the mission-critical functionality of the device.
Whether it’s a consumer product such as a smart watch, a smart city application or automotive telematics, the IoT will only go as far as the hardware allows. Today’s IoT enables people to find an open parking spot in a crowded city via a smart parking meter, a homeowner to turn off the lights or open the front door for a family member remotely – and can even alert family members if an older relative forgets to take their medication. By looking at how the connected world already affects our lives, we can begin to understand how invaluable the hardware driving it is.
We can’t talk about the IoT without discussing the Industrial Internet of Things (IIoT), which is where the smart factory comes in. IIoT represents the convergence of physical production systems with the communication and control of the virtual world. Responding to the need for shorter product lifecycles, rapid changes in demand and the growing requirement for product personalization, modern factories are beginning to leverage machinery and automation which can communicate with other equipment and even other manufacturing plants.
Driven by Manufacturing Execution Systems (MES) and Enterprise Resource Planning (ERP), these systems can quickly re-configure production schedules and anticipate bottlenecks and equipment problems in order to achieve drastically improved flexibility. In order to function successfully, these modern factories will depend on a variety of hardware components including sensors, embedded computers, machine-to-machine (M2M) communication modules, barcode scanners, 3D printers, gateways and other network equipment.
Given the functionality and environments in which they operate, IIoT devices will have different specifications and requirements than consumer-facing IoT products. Rather than sleek buttons and switches on delicate consumer electronics, industrial connected devices will require added durability and functionality. The ability to perform reliably in harsh environments, to function across wide temperature ranges and to have a long product lifecycle are key requirements for the switches used on today’s industrial machine interfaces.
Hardware is the common thread through all of our connected devices – and ultimately what will be responsible for pushing the IoT and IIoT to the next level. Whether it’s consumers hoping to control their house’s temperature from afar, or manufacturers looking to coordinate their heavy equipment, the world is getting a swath of new connected devices – and it’s the hardware contained within them that will ensure they keep working efficiently.
Mike Bolduc
Global Segment Manager
Industrial