Why Six Sigma is a Must at C&K (and Should Be for All Electronic Components Manufacturers)
By Jérôme Brochot | April 18, 2017
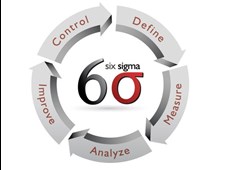
You probably all have heard about Six Sigma, or even attended some Green Belt or Black Belt trainings during these past few years. Is it just a management fashion that will pass, as others have before it, or is it going to last?
It is true that after the boom during the 2000s, with the strong involvement of top management leaders following the models of GE or Motorola, Six Sigma has now become something that we see less nowadays in corporate financial reports. But one of the reasons could be that it instead became a standard in many companies.
We should remember that it started before year 2000, even before the QS9000 quality automotive standard, (which was later on merged into ISO TS 16949 and recently changed to IATF 16949). When these automotive standards started to spread all around the world, some notions like GRR (repeatability and reproducibility for measurement systems), control plans, capability studies or FMEA became mandatory to many companies working directly as automotive suppliers. In addition, these were even accepted as a standard by many companies outside of the automotive world.
QS 9000 and Six Sigma combined their efforts in the development of these so-called “core tools.” But many companies, like C&K, continued to push toward even higher standards, using more complex statistical models and tools. With more and more data now available from all machines and processes, Six Sigma can be used easier than before to identify critical factors and track areas of improvement.
The need for Six Sigma in C&K can be easily understood using some figures and calculations:
C&K is making over 500 million switches a year. We have around 10 critical characteristics on every switch (including activation force, click ratio, coplanarity, electrical travel, etc.), which means over 5 billion opportunities for failure every year!
Let’s refer to the table below indicating the ppm level, depending on Sigma level:
Sigma Level |
CPK |
PPK |
PPM Level |
3 |
1 |
0,66 |
66 807 |
4 |
1,33 |
1 |
6 210 |
5 |
1,66 |
1,33 |
230 |
6 |
2 |
1,66 |
3,4 |
Standard quality requirements refer to Sigma levels of 3 or 4. If we take a Sigma level of 4, with a ppm level of 6210, we would find 6210 x 5 000 000 000/ 1 000 000= 31 050 000, or 31 million failures per year! It would, of course, be impossible to survive in 2017 with such a high level of failures.
When facing such an issue, implementing a 100 percent automatic end of line tester is usually a first answer, but the scrap cost in such a case would be just impossible to support for a company like C&K.
Only a combination of such a tester with Six Sigma level can eventually enable us to provide less than 1 ppm to our customers, while remaining competitive!
At C&K, all our processes were built and refined year after year, towards this goal. This is a never ending story and needs support and involvement at all levels in the organization, from top management to the people in different workshops.
We continue to train Yellow Belts, Green Belts and Black Belts, but moreover, we set up some very clear rules in any new design or in any production in order to make sure that the needed Sigma level will be achieved.
Six Sigma is no longer considered just a tool for quality; it’s a part of our DNA!